Best Practice HSE Management Systems: Essential for Energy Industry Success
- Admin Totaltec
- Mar 6
- 4 min read
7 March 2025, Georgetown, Guyana; In the high-risk environment of the energy industry, a robust Health, Safety, and Environmental (HSE) management system is business critical, in addition to being a regulatory requirement. For those 1,100+ Guyanese companies now in the Local Content Register, business success requires implementation of an HSE management system that aligns to oil and gas industry best practices. Implementing such a system delivers both top tier safety performance and business advantages.
Key Elements of a Best Practice HSE Management System
The following framework consisting of 8 elements, is based on one applied in the oil and gas industry, proven to ensure companies have robust HSE management systems that ensure the safety of their workers and performance of their organization. Its origins date to the 1988 North Sea Piper Alpha disaster, when major operators and the UK Government came together to make a step change in safety management.
While each Guyanese company will have its own HSE management approach, it can be mapped to, and audited against the following elements;
Leadership and Commitment: Senior management must visibly demonstrate commitment to HSE excellence through policy statements, resource allocation, and personal engagement.
Risk Management: Comprehensive processes for hazard identification, risk assessment, and implementation of controls across all operations.
Operational Controls: Detailed procedures and work instructions for high-risk activities, with clear roles and responsibilities.
Emergency Preparedness: Robust response plans for potential incidents, with regular drills and simulations.
Contractor Management: Processes ensuring contractors meet or exceed company HSE standards.
Incident Investigation: Systematic procedures for thorough investigation, root cause analysis, and implementation of corrective actions.
Performance Measurement: Clear metrics tracking both leading and lagging indicators of HSE performance.
Continuous Improvement: Mechanisms for regular review and enhancement of the system based on performance data and lessons learned.
To be successful working in the energy industry, Guyanese companies must understand that HSE excellence isn't an add-on program—it's fundamentally integrated into every business process," says Lars Mangal, CEO of TOTALTEC, Inc. "When we developed our HSE management system, we recognized that as well as robust processes, it was critical to create a genuine culture of safety that drives operational excellence.
Auditing Current Systems Against Best Practices
Guyanese companies should be able to assess their existing HSE management systems against the above elements. They will not necessarily follow exactly these 8 elements. However, each point should be addressed within a company management system. Such management system standards offer the benefits of:
Gap analysis comparing current practices against international standards (ISO 45001, IOGP 510)
Benchmarking against other local companies and industry leaders, including outside Guyana
Internal cross-functional audits involving operational personnel, powerful for knowledge sharing
External specialist audits providing objective assessment, longer term possibly involving the Guyana government
Audits should evaluate both system design and implementation effectiveness. Documentation review should be complemented by field observations and personnel interviews across all organizational levels.
Developing an Implementation Plan
Based on audit findings against these 8 elements, companies should develop a phased approach to bring their HSE management system up to industry best practice standards:
Prioritize gaps based on risk assessment
Set specific, measurable objectives with defined timelines
Assign clear accountability for implementation actions
Secure necessary resources, particularly for technology systems
Establish regular progress reviews
Engage external specialist input to provide objective review, provide an outside perspective
"When TOTALTEC was formed back in 2016, we prioritized improvements that addressed our highest operational risks first," Mangal explains. "This focused approach delivered immediate safety benefits while building momentum for our wider implementation and business growth. In the years since we have adapted our management system in line with the evolution of our business, always anchoring to industry best practices. Our results show it works.”
Training Forms Part of the Plan
Anytime changes are made to management systems, training plans must be made for effective implementation. The elements of associated training for evolving HSE management systems will include:
Leadership training for executives and managers on HSE leadership principles
Management system awareness training for all personnel
Specialized training for HSE professionals on system elements and tools
Risk assessment methodology training for operational supervisors
Internal auditor training for cross-functional audit teams
Depending on the scope of operations, Guyanese companies will have additional specific training requirements to build necessary competencies. Organizations should integrate HSE competencies into role profiles and ensure these skills are regularly assessed, in addition to forming part of performance reviews.
The most successful Guyanese companies will approach HSE as a shared responsibility across the organization. In many cases, this will require a cultural shift, supported by management commitment. With robust systems and processes, such HSE best practices based management systems will deliver the dual benefits of workforce safety and enhanced business performance.
Learn more about Guyanese companies building the energy industry:
Visit the Ministry of Natural Resources website 'Petroleum Management Program at
Read a recent OilNow article on companies now in the Local Content Register, as well as estimated spend to those companies.
About TOTALTEC
TOTALTEC Inc. is a 100% Guyanese owned and operated company focused on building capacity in Guyana. Included are manpower - both experts and workers, project management, training services - including eLearning, classroom and practical, and facilities services. Facilities include modular offices/shop/lab fabrication, open yards and storage areas and the CAMPBOSS Hospitality Group, which both builds and services custom designed facilities. Partnerships prioritize products and services to grow from, creating Guyanese led companies, for example Jaguar Oilfield Services.
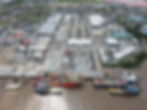